一、技術名稱:水溶液全循環尿素節能生產工藝技術
二、適用范圍:水溶液全循環尿素生產裝置改造或新建
三、與該節能技術相關生產環節的能耗現狀:
目前,我國氮肥行業的噸尿素產品單耗為:氨580㎏、蒸汽1250㎏、循環水140m3、電140kWh,合成轉化率65%。
四、技術內容:
1.技術原理
1)高壓合成工序:
來自氨庫的原料液氨,經液氨泵加壓到20~23MPa后送往液氨預熱器,被加熱到70℃分為兩路,一路約為總量80%的NH3、103℃甲銨液和來自CO2壓縮機20~23MPa的 CO2一起進入合成塔塔頂分布器;另一路約20% 的NH3通過尿素合成塔底部進入,在塔內完成等溫高壓合成反應,反應產物從塔的頂部出來。
工業生產尿素的反應分兩步進行,第一步由氨和二氧化碳反應生成中間產物氨基甲酸銨(簡稱甲銨),其反應式為:
2NH3(液)+CO2(氣)=NH4COONH2(液)+ Q1
第二步由甲銨脫水生成尿素,其反應式為:
NH4COONH2(液)=CO(NH2)2(液)+H2O(液)-Q2
第一步反應是一個可逆的強放熱反應,生成氨基甲酸銨的反應速度比較快,容易達到化學平衡,且達到化學平衡后二氧化碳轉化為氨基甲酸銨的程度很高。第二步反應是一個可逆的微吸熱反應,需要在液相中進行,反應速度慢,需要較長時間才能達到化學平衡,即使達到化學平衡也不能使全部氨基甲酸銨都脫水轉化為尿素。
2)循環回收工序
從合成塔出來的反應混合物先后經過中壓分解吸收(壓力1.7 MPa)和低壓分解吸收(壓力0.3 MPa)后,尿素濃度達到67%左右,溫度為140℃,然后送入蒸發系統;尿素尾氣通過高效安全的尾氣凈氨處理后(氨含量小于1%)放空。
3)蒸發工序
從低壓循環系統來的尿素溶液送入逆流降膜式預濃縮器,以中壓分解氣作熱源進行預濃縮,將尿液濃度從67%提高到85%;用膨脹蒸汽和蒸汽冷凝液作熱源對85%尿液進行兩段加熱進行再濃縮,使尿液濃度從85%提高到95%,完成對尿素的一段蒸發。出一段蒸發器的尿液再經過二段蒸發加熱器,濃縮至99.6%左右,送至尿素造粒塔進行造粒。
4)解吸、水解工序
碳銨液由解吸泵送至解吸水解系統,采用蒸汽加熱氣提,使塔底排出的解吸凈水中尿素及氨含量≤5ppm;解吸水解塔底出來的188℃解吸凈水、解吸水解塔頂出來的160℃的解吸氣分級利用于尿素分解工序,利于節省蒸汽、維持系統水平衡。
2.關鍵技術
1)液相逆流換熱式等溫合成塔和尿素合成塔的優化運行;
2)二次加熱-降膜逆流換熱應用于中壓分解工藝;
3)三段吸收-蒸發式氨冷-低水碳比尿素中壓回收工藝;
4)一段蒸發系統低位能熱的利用;
5)尾氣凈氨新工藝;
6)高效尿素低壓分解回收新工藝;
7)節資-節能型尿素廢水處理系統。
3.工藝流程
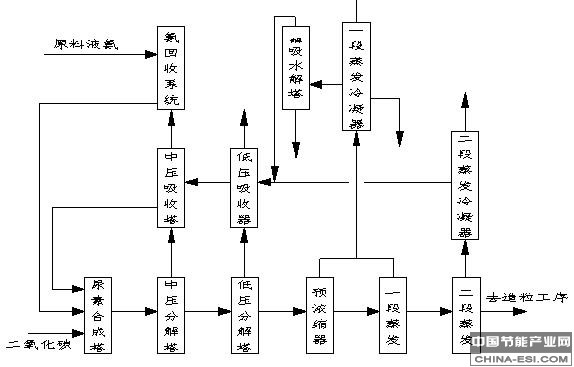
水溶液全循環節能尿素生產工藝流程圖
五、主要技術指標:
1)噸尿素單耗:氨570㎏、蒸汽905㎏、循環水77m3、電125kWh;
2)合成二氧化碳轉化率72%;解吸后凈水中氨和尿素含量<5ppm。
六、技術應用情況:
該技術已通過四川省科技廳的技術鑒定,并成功應用于1000t/d尿素生產裝置,節能效果顯著,安全環保,生產設施先進。
七、典型用戶及投資效益:
典型用戶:四川金象化工產業集團股份有限公司
1)建設規模:400t/d尿素生產裝置的技術改造。主要技改內容:利用節能型尿素生產技術對日產400噸尿素裝置中低壓分解回收等系統進行節能改造,主要技改設備包括精洗器、預蒸發器和外冷器等。節能技改投資額960萬元,建設期6個月。年節能9145tce,年節能經濟效益799萬元,投資回收期約1.2年。
2)建設規模:1000t/d尿素生產裝置新建項目。主要技改內容:新建1000t/d尿素水溶液全循環生產裝置,主要設備包括液相逆流換熱式尿素合成塔、尿素中壓吸收塔、臥式浸沒式尾氣吸收器、蒸發式冷凝器和解吸水解塔等。節能技改投資額15437萬元,建設期1年。年節能2.1萬tce,節能經濟效益2310萬元,投資回收期4年。
八、推廣前景和節能潛力:
水溶液全循環節能尿素生產技術適合新建尿素生產裝置和對現有水溶液全循環裝置進行節能增產改造,改造工作量小,投資較低,生產能力有較大提高,并可大幅度降低原材料消耗、消除環境污染,經濟效益和環保效益顯著。在國內水溶液全循環尿素生產企業進行節能增產改造,有廣闊的推廣前景。
目前我國尿素產能約6500萬t/a,其中50%是水溶液全循環工藝,若其中的30%采用水溶液全循環節能尿素生產技術進行改造,年可節能約70萬tce。
深入專題了解:國家重點推廣節能技術目錄
|