一、技術名稱:火電廠煙氣綜合優化系統余熱深度回收技術
二、適用范圍:燃煤火電機組
三、與該節能技術相關生產環節的能耗現狀:
火力發電廠消耗我國煤炭總產量的50%,其排煙熱損失是電站鍋爐各項熱損失中最大的一項,一般在5%~8%,占鍋爐總熱損失的80%或更高。排煙熱損失的主要影響因素是鍋爐排煙溫度,一般情況下,排煙溫度每升高10℃,排煙熱損失增加0.6%~1.0%,發電煤耗增加2g/kWh左右。我國現役火電機組中,鍋爐排煙溫度普遍維持在125~150℃左右水平,褐煤鍋爐為170℃為左右,排煙溫度高是一個普遍現象,由此造成巨大的能量損失。
對于已經投運的鍋爐,經過燃燒優化來降低排煙溫度的幅度非常有限,省煤器和空氣預熱器的改造因受到空間的限制,降低排煙溫度的幅度也很小,同時尾部受熱面的低溫腐蝕也限制了排煙溫度的大幅降低。因此,獨立于原有鍋爐系統之外的排煙余熱回收系統成為節能降耗的首選。
四、技術內容:
1.技術原理
電站鍋爐排煙余熱深度回收利用系統安裝在除塵器之后、脫硫塔之前的煙道中,可以最大程度地降低煙氣溫度,使煙氣溫度再降低40~50℃。在一些采用濕煙囪或煙塔合一等最新煙氣排放技術的電廠,脫硫塔入口煙溫可降低到85℃左右,使煙溫達到最佳脫硫效率狀態,大大減少脫硫塔的冷卻水耗。
排煙余熱回收系統所吸收的能量可以用來加熱凝結水,或通過暖風器加熱空氣提高送風溫度,從而減少低壓加熱器或者暖風器的抽汽量,增加汽輪機做功,提高機組效率。
2.關鍵技術
1)排煙余熱回收裝置即煙氣冷卻器的設計; 2)排煙余熱回收裝置即煙氣冷卻器的防腐; 3)排煙余熱利用系統即低壓給水加熱器或者暖風器的設計; 4)熱力系統優化設計和控制。
3.工藝流程
工藝流程見圖1,循環介質(水)在循環水泵5的作用下,通過入口集箱3進入煙氣冷卻器2,吸收尾部煙道1中的煙氣余熱后溫度升高,經出口集箱4流出。當環境溫度較高時(例如在夏季),導向閥13切換到加熱給水狀態,空氣加熱器閘閥8全關,給水加熱器閘閥6全開。經出口集箱4流出的高溫循環介質(水)進入給水加熱器14,把在煙氣冷卻器2中吸收的熱量釋放給低壓給水后開始下一個循環。凝結水經過分水調節閥10、11、12進入給水加熱器14,吸收循環介質(水)釋放的熱量,溫度升高后進入除氧器。分水調節閥10、11、12可以改變各級(1#、2#、3#)低壓加熱器的分水比,根據實際運行情況進行優化調節。當環境溫度較低時(例如在冬季),導向閥13切換到加熱冷空氣狀態,空氣加熱器閘閥8全開,給水加熱器閘閥6全關。經出口集箱4流出的高溫循環介質(水)進入空氣加熱器7,把在煙氣冷卻器2中吸收的熱量釋放給送風后開始下一個循環,冷空氣溫度升高后進入空氣預熱器繼續加熱。
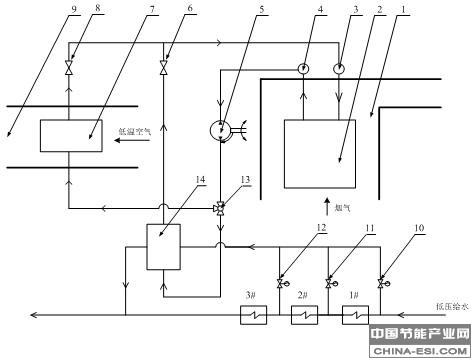
煙氣綜合優化系統余熱深度回收工藝流程圖
1為尾部煙道,2為煙氣冷卻器,3為進口集箱,4為出口集箱,5為循環水泵,6為給水加熱器閘閥,7為空氣加熱器,8為空氣加熱器閘閥,9為風道,10~12為低壓加熱器分水調節閥,13為余熱利用導向閥,14為給水加熱器。
五、主要技術指標:
電站鍋爐采用該排煙余熱深度回收系統后,發電煤耗可以降低2~3g/kWh。
六、技術應用情況:
該技術已獲得國家專利,目前已經在華能集團下屬的兩個火力發電廠應用。
七、典型用戶及投資效益:
典型用戶:華能國際電力股份有限公司井岡山電廠
1)建設規模:300MW火電機組。主要技改內容:在增壓風機之后脫硫塔之前的煙道增加煙氣冷卻器,把給水從6#低壓加熱器前通過管道引入煙氣冷卻器,加熱后回到5#低壓加熱器,使排煙溫度從152℃降低到108℃,低壓給水從83.8℃加熱到103.7℃,主要設備包括煙氣冷卻器、控制系統、閥門和管道。節能技改投資額640萬元,建設期45天。年節能3990tce,年節約費用319.2萬元/年,投資回收期2年。
八、推廣前景和節能潛力:
國內現有的300-1000MW機組大部分采用濕法煙氣脫硫系統,要求進入脫硫塔的煙氣溫度在80℃左右,因此鍋爐排煙中的部分余熱未被充分利用,通常使用噴水、GGH(氣氣換熱器)降溫,造成了熱量的損失。排煙余熱深度回收利用技術可以把這部分熱量回收用于加熱給水、送風。改造后發電煤耗平均降低約2g/kWh。截止到2009年12月,我國火電裝機容量為6.52億kW。據此推測,如果有50%的火電廠進行排煙余熱深度回收利用改造,年運行時數平均按照5000小時計算,每年節能320萬tce,節能潛力巨大。
深入專題了解:國家重點推廣節能技術目錄
|